I slutet av 2008 började strömlinjestrategin Lean införas hos Vossloh.
– Vi ville öka vår effektivitet. Flera företag har drivit ett framgångsrikt Leanarbete och vi ville prova. Idag är metoden genomförd på alla avdelningar, säger Vosslohs Lean-coach och koordinator Fredrik Andersson.
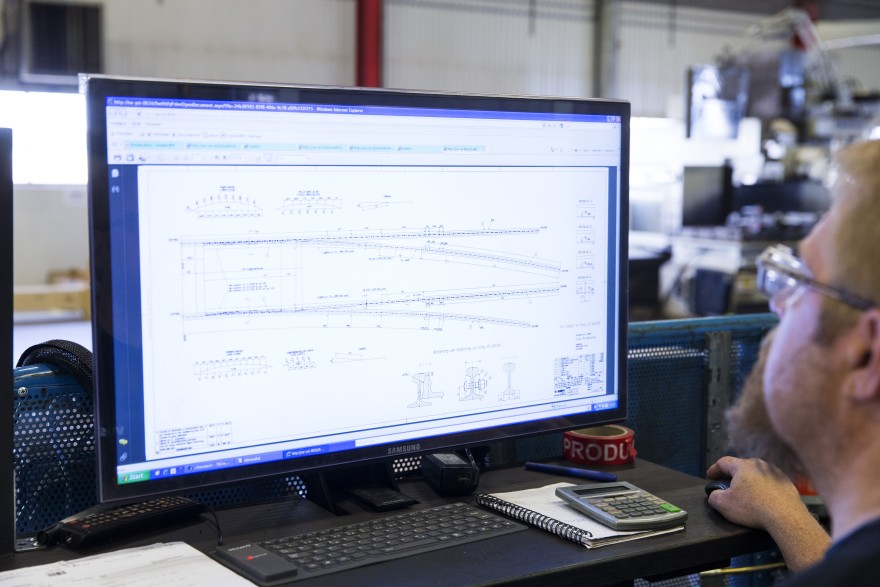
– Fördelarna är naturligtvis att vi blir mer lönsamma med ett snabbt och effektivt arbetssätt, men det uppstår även viktiga mjuka värden då alla involveras. Det skapar en förståelse för varandra och processen. Lean är ett enkelt sätt att se hur det går för oss, vilka problem som finns och vilken support som behövs. Efterhand som förbättringar genomförs upptäcker vi nya saker, säger Fredrik Andersson.
Bästa arbetssätt
Varje avdelning - exempelvis order, konstruktion, planering eller offert - har nu ett standardiserat och dokumenterat bästa arbetssätt. Alla arbetar enligt 5S-metoden för att hålla ordning genom att systematisera, standardisera och sortera. Rätt sak på rätt plats, helt enkelt. Det ska vara lätt att hitta material för att på så sätt skapa säkerhet.
Avdelningarnas arbete presenteras på en produktionstavla. Mättal förs in var dag vilket gör att det går snabbt att upptäcka om det uppstår problem och behövs support. Under en treveckorsperiod har produktionstavlorna synats dagligen för att göra arbetet ännu effektivare.
– Om vi upptäcker ett problem sätter vi oss ner och löser det direkt. För vart problem vi löser beräknar vi vinsten. Exempelvis har vi de två senaste veckorna sparat 190 timmar i merjobb.
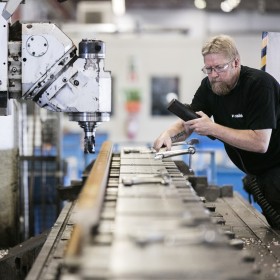
Enstycksflöde används, där en order eller produkt i taget hanteras istället för flera parallellt. Det gör att inga lager behövs utan en order i taget skeppas.
– Vi har också sparat tid i huvudproduktionsflödet, där det tidigare gick åt mycket tid för att flytta material. Där ledtiden tidigare var 45 dagar är vi nu nere på 3 dagar. Vi har lyckats genom att skapa ett flöde som hanterar en order i taget. Vi blir 10-20 procent bättre för vart år.
Finalist för pris
Förra året var Vossloh en av fyra finalister till Svenska Leanpriset för sitt arbete med att skapa en ny orderavdelning. I år tävlar man internt med samma organisationsförändring.
– Tidigare hade vi problem med våra orderbekräftelser. Kunden ville ha bekräftelse inom fem dagar vilket vi inte klarade. Då vi såg att arbetet inte var standardiserat utan föll mellan stolarna skapade vi en orderavdelning med ett nytt arbetssätt.
– Nu sitter denna tvärfunktionell grupp som arbetar med fastlagda rutiner, 5S, enstyckshantering och ökad synlighet. Genom att sitta tillsammans några timmar var dag och hanterar registrering och kundorder underlättas samarbetet. Idag tar det i snitt två dagar innan kunden fått sin bekräftelse, säger Fredrik Andersson.
Ett av verktygen för att driva Lean är event, tvärfunktionella arbetsgrupper som samlas under en vecka för att lösa ett specifikt problem. Detta görs cirka 20 gånger per år.
– Tre veckor innan eventet bestäms syfte, startläge - var står vi idag med mättal - och målläge - vart vill vi? Under eventet benas problemet upp och lösningar föreslås och testas. Sedan görs en implementering som följs upp med mättal. Eftersom eventet avslutas med att gruppmedlemmarna får berätta om sina insikter blir det en lärande process. Alla i gruppen är med under samma förutsättningar, att inte ta tillvara allas kreativitet vore ett slöseri. Samtidigt skapas en grogrund för tillväxt bland personalen och internrekrytering.
Nu breddas Leanarbetet. En framtidskarta med processbeskrivning har tagits fram, där de närmaste 18 månaderna presenteras. Nästa steg är att involvera leverantörerna.
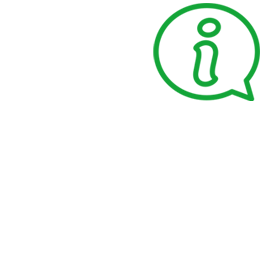
Lean production
Lean startade hos Toyota efter andra världskriget. Syftet är att eliminera slöseri genom att upptäcka och ta bort alla faktorer i en process som inte skapar värde för kunden. Fokus ligger på väntetider, rörelser, om- och överarbete, överproduktion, lager, outnyttjad kreativitet och transporter. Lean-arbete anpassas efter verksamhetens behov och förutsättningar. Det fungerar även i tjänsteföretag, och är vanligt inom sjukvården.
sv.wikipedia.org/wiki/Lean_production
Mål